ABOUT SHAMROCK
- Aluminum Die Cast Parts up to 11 pounds
- Shamrock Industries manufactures Aluminum and Zinc Die Cast Parts
- Zinc Die Cast Parts up to 5 pounds
- Shamrock Industries can provide “Certificate of U.S. Manufacture”
- Shamrock Industries provides part design assistance
- U.S. Manufacturer of Aluminum and Zinc Die Castings
- Shamrock Industries is a custom die cast part manufacturer --- no proprietary products to prioritize in production
- Conservative Culture – no debt and low overhead enable aggressive pricing
- Flexible manufacturing – both short run/ low volume and high volume manufacturing of aluminum and zinc die cast parts
- Secondary machining services, finishing, assembly, and special packaging as desired
- No set-up charge on transferred or new tools
- Located in Texas, Shamrock Industries can logistically support customers with die cast parts throughout North America
- Die cast parts for pressure tight applications
- Aluminum and Zinc die cast parts delivered on-time
- Low Cost Die Castings manufactured in Fort Worth, Texas
- Close tolerance die cast parts in Aluminum and Zinc alloys
- Short lead times to reduce your inventory costs
- Dependable quality die cast parts
- Integrity… we protect your Intellectual Property
- “C of C” with every shipment as requested
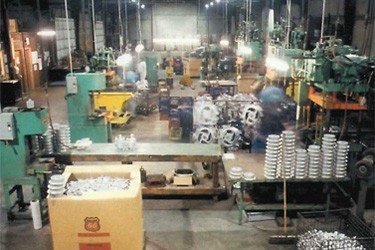
Our Services
Manufacturing Services of Shamrock Industries: With the culture of Shamrock Industries coupled with the size of our company, we are a flexible and responsive supplier of aluminum and zinc die cast parts.
- Short run/ low volume and high volume manufacturing of aluminum and zinc die cast parts
- Secondary machining services, finishing, assembly, and special packaging as desired
- Painting
- Plating
- High Pressure Aluminum and Zinc Diecasting
- Aluminum Die Cast Parts up to 11 pounds
- Zinc Die Cast Parts up to 5 pounds
- Aluminum alloys 360, 380, 383, 390, and 413
- Zinc alloys Z3, Z5, and ACCU Zinc
- 11 Die Cast Machines, 80 to 900 ton die cast machines
- No proprietary products to interfere with production scheduling
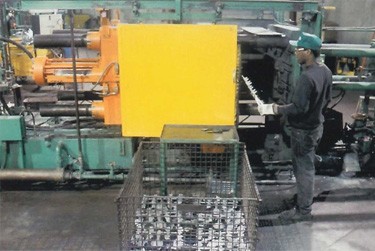
Quality Die Cast Parts from Shamrock Industries: Shamrock Industries has grown by providing consistent quality aluminum and zinc die cast parts. Quality starts with a mind set for "expectations of excellence" from our employees to our suppliers. Each one of our employees is aware of the characteristics of your casting. This is consistent with the definition as stated in ISO 8402-1986. Our Q.U.E.S.T. (Quality through United Effort Secures Tomorrow) is our mission to satisfy our customers' needs. Shamrock Industries retains on file all traceability of your tooling to the alloy that is used to produce your casting. We are flexible in our ability to cater to specific programs to enhance the integrity of your products. Quality at every phase represented in insuring a quality die cast part…
- Engineering and application parameters understood prior to tooling program and production
- Your quality expectations are understood and adhered to for your aluminum and zinc die cast parts
- Dies inspected prior to production of die cast parts
- First article inspection approval prior to release for production
- Intermittent inspection during production of die cast parts
- Inspection at secondary operations such as trimming and machining
- Final inspection prior to shipping your die cast parts
- C of C of alloys with every shipment as requested
- Certificate of U.S. Manufacturer as requested
- Project Management and Continuous Improvement
- Coordinate Measuring Machine
- N.A.D.C.A. Products Standard for Die Castings
Tooling to Manufacture Die Cast Parts: The design and manufacturing of Die Cast Tooling, Dies, or Molds is critical to the final quality of your die cast component parts. The type/ form of tooling best suited for your die cast parts will depend on the quantity, part design and size, and perhaps mating parts (family die/ mold). In addition to the die/ mold to cast your component parts, it may also increase quality and reduce part cost by utilizing a trim die.
Manufacturing New Die Cast Tooling: Shamrock Industries understands that tool design and manufacturing is critical to successful and timely production of aluminum and zinc die cast parts. Because Shamrock Industries services numerous industries with diverse part designs, we have found it beneficial to the customer for Shamrock Industries to obtain tooling quotations from our qualified tooling craftsmen located in the U.S. and present our recommendations to the customer. Commercial transactions for tooling are directly with the customer and the toolmakers. Shamrock Industries interfaces with both the client and toolmaker on design consideration and schedule of initial first article die cast parts. Typically, first article die cast parts are manufactured within a couple days of receiving the new die cast tool. Tooling manufactured in U.S. also helps control of your intellectual property and market introduction of new products.
Transferring of Die Cast Tooling: Shamrock Industries welcomes your existing die cast tools and molds. Shamrock Industries can accommodate insert dies and unit dies utilizing our mold bases, family mold tools, and full Class “A” die cast tooling. When your die cast tooling arrives at Shamrock Industries we will immediately inspect and photograph and advise you of status tooling. Any needed repair/ maintenance will be performed and first articles provided immediately for your review. There is no charge for running first articles on transferred tooling for aluminum and zinc die cast parts.
Maintenance of your tooling: Tooling maintenance and minor modifications are performed in-house. Shamrock Industries takes great care in maintaining your tooling to insure optimal quality of die cast parts and life of tools.
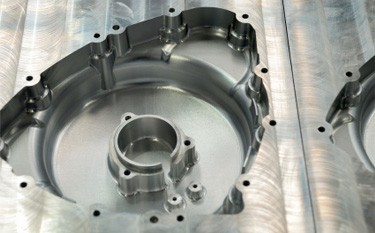
Applications/ Markets for Die Cast Parts
Small Engine, Electric motors, HVAC, Lock components, gas valves, lighting, medical and dental equipment, appliances, Sporting goods, transportation, food equipment, furniture, lawn & garden, computer, electronics, hardware
Aluminum and Zinc Die Cast Parts versus Plastic Injection Molded Parts
- Die cast parts will have better mechanical strength than most plastics
- Die cast parts are more resistant to heat and thermal cycling
- With the same dimensions, die cast parts are stronger than plastics
- Die cast parts can be thinner and lighter than plastic equivalent and still meet mechanical requirements
- Thin-walled die castings can accommodate stresses where a comparable plastic parts cannot succeed
- Die cast parts are more dimensionally because of the stiffness of the alloys versus plastics
- Die cast alloys are inherently electrically conductive
- Die cast alloys provide inherent shielding from EMI
- Die cast alloys are 1,000 times more thermally conductive than plastics
- Die cast alloys resist creep better than plastics
- Die cast parts can hold closer tolerances than plastics because of stiffness and thermal stability
- Die cast parts are ‘green’ --- over 95% of aluminum die cast parts produced in North America use recycled aluminum
- Die cast parts can be plated for aesthetics
- Die cast parts have high yield and impact strength
- Die cast alloys are not affected by UV rays
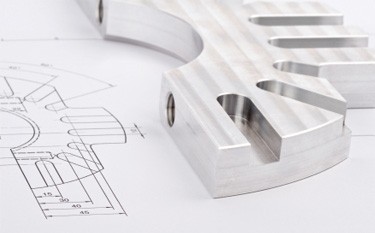
Benefits of Aluminum and Zinc Die Cast Parts
- High quality surface finish attainable on aluminum and zinc die cast parts
- Numerous alloys available for specific applications
- Ideal for pressure tight appications
- EMI (electro magnetic interference) shielding
- Electrically conductive die cast parts
- Thermal conductivity
- Weatherability
- Thermal Stability
- Low cost
- Up to 1,000,000 parts produced on Class ‘A’ Die Cast Tooling
Benefits of U.S./ American Source for your Die Cast Parts
- Minimize product to market time
- Control of I.P. and market intro
- Quality
- Material compliance and certification
- Communication directly with manufacturer --- no middle man
- Logistics
- Reduction of time to market
- Lower inventory – less than 2 week lead time average
- Only parts for you from your tools
- No prepayment of parts; 1% 10, net 30 day trade terms
- No shortcuts on tooling quality
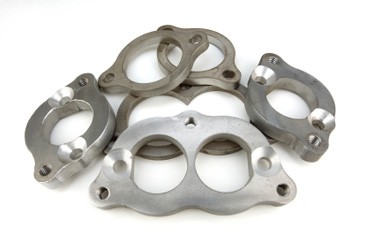